WHITE PAPER - The Definitive Choice in Dense Phase Pneumatic Conveying: Why Dome Style Valves Are Essential Over Butterfly Valves
- John Forbes
- Jul 7
- 6 min read
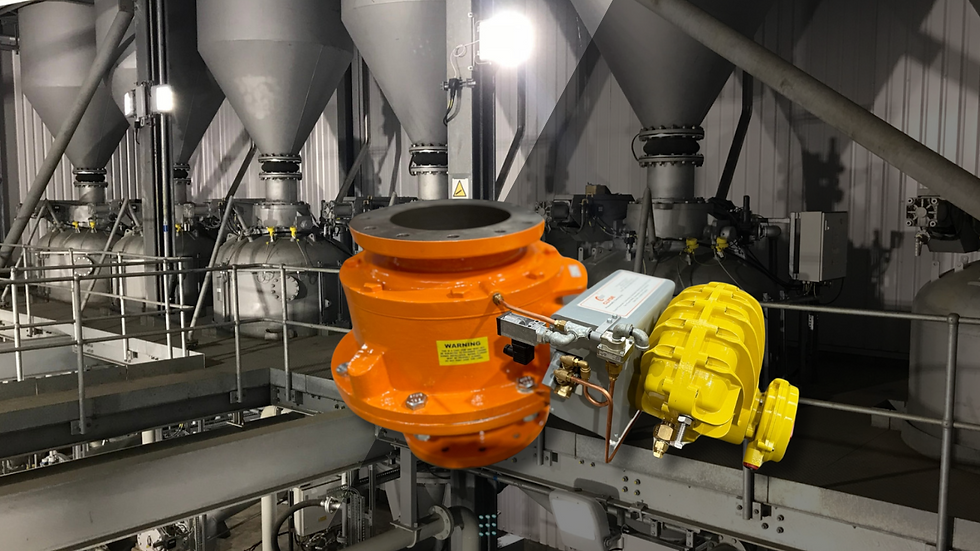
Introduction
In the complex landscape of bulk material handling, dense phase pneumatic conveying stands as a highly efficient method for transporting a diverse range of materials, particularly those that are abrasive, fragile, or require precise control. The success and longevity of such systems hinge on the performance and durability of every component within the conveying line. Among these, the isolation or control valve plays a disproportionately critical role. While some may consider butterfly valves as a seemingly straightforward and economical option for various industrial applications, their inherent design limitations become acutely apparent and significantly detrimental when integrated into a dense phase pneumatic conveying system.
At Delta Ducon, our over 100 years of experience in pioneering bulk material handling solutions have provided us with an unparalleled perspective on valve technology and its profound impact on system integrity and operational efficiency. Our deep engineering expertise, forged through decades of designing and implementing robust systems for the most demanding industries—from cement and mining to steel and power generation—consistently leads us to a clear and unequivocal conclusion: for optimal, reliable, and cost-effective dense phase pneumatic conveying, the dome style valve is not just an option; it is an indispensable component. This white paper will thoroughly examine the fundamental differences between butterfly valves and dome style valves, elucidating why the inherent design and operational advantages of a dome style valve render it the unequivocally superior, and indeed essential, choice for all dense phase applications.
Understanding Dense Phase Pneumatic Conveying Dynamics
Dense phase pneumatic conveying operates by transporting bulk materials in discrete slugs or plugs, often at lower velocities but higher pressures compared to dilute phase systems. This method is particularly favored for:
Abrasive Materials: The lower conveying velocities significantly reduce erosive wear on internal pipeline surfaces and components, extending their operational lifespan.
Fragile Materials: The gentler, lower-velocity movement minimizes particle degradation, attrition, and breakage, preserving material integrity.
High Capacities and Long Distances: Dense phase systems are highly effective at efficiently moving large volumes of material over extended conveying paths.
Minimized Dust Emissions: As a fully enclosed and pressure-sealed system, it inherently offers superior dust control, enhancing workplace safety and environmental compliance.
The fundamental success of a dense phase system is predicated on its ability to accurately form and maintain these distinct material slugs, which necessitates precise control of both air and material flow, coupled with absolutely tight seals to contain the elevated conveying pressures. It is at this juncture that the selection of the correct valve becomes critically important.
The Inherent Limitations of Butterfly Valves in Dense Phase Applications
A conventional butterfly valve employs a disc that rotates, typically 90 degrees, around a central shaft to either block or allow flow. While these valves are widely adopted across various industrial sectors for general flow regulation or fluid/gas isolation, their application within dense phase pneumatic conveying systems reveals significant and often costly drawbacks:
Compromised Sealing in Abrasive Environments: The foundational design of a butterfly valve relies on a resilient, soft seal (e.g., rubber, PTFE) positioned around the disc to achieve a tight shut-off. In the presence of abrasive bulk solids, these particles are invariably entrapped between the rotating disc and the static seal during the closing sequence. This unavoidable interaction leads directly to:
Rapid Seal Wear: Abrasive particles swiftly abrade and degrade the integrity of the soft seal, leading to premature failure and operational leakage.
Incomplete Shut-off: Worn seals result in material leakage (contributing to fugitive dust) and, critically for dense phase, constant air leakage.
Loss of Pressure Integrity: Air leakage compromises the delicate pressure differential that is absolutely essential for efficient and controlled dense phase operation. This can lead to increased air consumption, reduced conveying efficiency, inconsistent material flow, and a heightened risk of pipeline blockages.
Obstruction to Material Flow: When a butterfly valve is in the open position, its disc invariably remains partially within the flow path. For bulk solids, especially those conveyed in coherent dense phase plugs, this remaining disc presents a tangible and disruptive obstruction.
Accelerated Wear: The continuous impact and direct abrasion of the conveyed material against the exposed disc and shaft lead to rapid degradation of these components.
Material Buildup: Sticky or cohesive materials can readily accumulate on the disc, hindering full closure or opening, and potentially causing blockages.
Turbulence and Degradation: The obstruction creates unwanted turbulence within the material flow, which can break up material slugs, increase particle attrition and degradation, and contribute to additional erosive wear downstream.
Inadequate Positive Isolation: Due to the cumulative effects of potential material buildup on the disc and the rapid degradation of the soft seal, a butterfly valve fundamentally cannot provide a truly positive and absolute isolation within a high-pressure dense phase system. This means it may fail to fully prevent residual material flow or maintain complete air pressure containment when nominally closed, thereby compromising operational safety and precise process control.
Elevated Maintenance Requirements and Downtime: The confluence of rapid component wear, persistent leakage, and the propensity for clogging means that butterfly valves, when misapplied in dense phase operations, demand frequent and intensive maintenance. This directly translates into significantly increased and often unscheduled downtime, leading to substantial operational expenses and lost production.
The Superior Solution: The Dome Style Valve for Dense Phase
The dome style valve, often associated with dense phase conveying systems due to its robust and unique design, stands out as the optimal choice. Delta Ducon's expertise with this valve style, particularly from our heritage with Clyde Pneumatic Conveying, showcases why this valve is engineered for the precise demands of dense phase applications.
The core principle of a dome style valve is a movable, inflatable seal that provides a perfect closure and a full-bore opening. Here’s why it’s unequivocally better for dense phase systems:
Achieves a Pressure-Tight Seal: This is the most significant advantage. The dome style valve operates with a unique inflatable sealing mechanism.
When the valve closes, the spherical dome (the closing element) rotates until it seats against a circular seal.
Once seated, an inflatable pressure seal expands to create a completely pressure-tight seal against the dome. This seal is energized only when the valve is fully closed and the dome is stationary and protected.
This design ensures zero leakage of both air and material, which is absolutely critical for maintaining the high pressures and precise air control required for efficient dense phase conveying.
Protected Seal and Minimal Wear: Unlike a butterfly valve where the seal is continuously exposed to the material flow, the dome style valve's inflatable seal is retracted out of the material stream when the valve is open and during the dome's rotation.
This "protected seal" design means the seal is only in contact with the dome when the valve is closed and static.
As a result, the seal is never exposed to the abrasive action of the conveyed material. This dramatically extends seal life, even with highly abrasive materials like sand, cement, or coal.
Full, Unobstructed Bore: When the dome style valve is fully open, the spherical dome retracts completely into the valve body, creating a full, unobstructed bore.
This provides a smooth, unimpeded flow path for the dense phase material slugs.
There is no material impact or abrasion on internal valve components in the open position, unlike a butterfly valve where the disc remains in the flow path.
This full bore design ensures maximum throughput, minimizes material degradation, and prevents blockages or material buildup that can plague other valve types.
Positive Isolation: The combination of the dome's mechanical closure and the inflatable seal provides a truly positive and reliable isolation. This is essential for safety, maintenance procedures, and precise process control in pressure conveying systems.
Exceptional Durability and Low Maintenance: Because the seal is protected and the dome itself is typically made of robust, wear-resistant materials, dome style valves exhibit exceptional durability in abrasive dense phase applications.
The absence of wear during operation translates to significantly extended service intervals and lower maintenance requirements compared to butterfly valves.
This leads to maximized system uptime and a lower total cost of ownership.
Delta Ducon's Expertise and the Dome Style Valve
Delta Ducon's long-standing heritage with Clyde Pneumatic Conveying has instilled in us a deep understanding and appreciation for the critical role of the dome style valve in dense phase systems. Our commitment to this valve style is a direct embodiment of this expertise. We recognize that for dense phase applications, particularly those involving abrasive, hot, or fine materials, relying on anything less than a dome style valve is a compromise that will lead to inefficiency and increased operational costs.
Our engineers integrate the dome style valve into our comprehensive dense phase pneumatic conveying solutions with confidence, knowing it provides:
Unmatched Sealing Performance: Ensuring system pressure integrity for efficient, low-velocity conveying.
Superior Wear Resistance: Protecting the most vulnerable valve components from abrasive materials.
Unimpeded Flow: Maximizing throughput and minimizing product degradation.
Reliable Operation: Reducing the need for frequent maintenance and minimizing unscheduled downtime.
Conclusion
For any dense phase pneumatic conveying application, especially those handling challenging materials, the choice of valve is paramount. While a butterfly valve may seem like an initial cost saving, its inherent design flaws make it fundamentally unsuitable for the high pressures and abrasive environments of dense phase. The dome style valve, with its protected inflatable seal and full-bore design, offers the only truly robust, reliable, and cost-effective solution. Delta Ducon's century of experience and our proven expertise with the dome style valve exemplify why this is not just a preference, but a requirement for optimizing all your dense phase pneumatic conveying systems.
Delta Ducon, LLC 11 General Warren Blvd. Malvern, Pa 19355-1216 U.S.A Phone: 610.695.9700 Toll Free: 1.800.238.2974 Fax: 610.695.9724 www.deltaducon.com